Related Articles
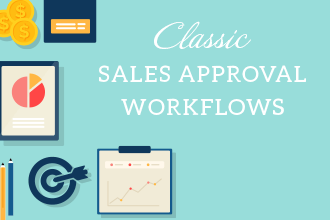
5 MINUTES READ
What is Sales Workflow? | 4 Classic Sales Approval Workflows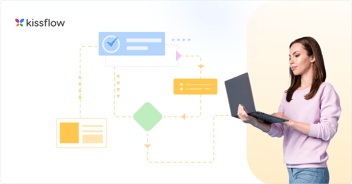
5 MINUTES READ
10 Perfect Workflow Examples for Business Processes 2025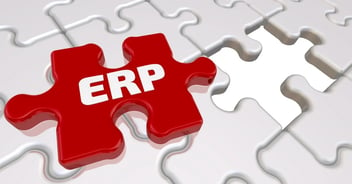
5 MINUTES READ
How Kissflow Simplifies ERP WorkflowsTeam Kissflow
Updated on 15 Apr 2025 • 5 min read
Inefficient processes are one of the biggest reasons causing a drip in businesses’ annual revenue. To turn this around, processes must be digitized. Digital workflow promote control of every aspect of a business, help optimize operations, and cut down costs. They are a form of quality assurance; they create repeatable business processes for constantly building high-quality products.
When manufacturing workflows are efficient, they help companies reduce waste and cut costs—which is what Industry 5.0 is all about. A manufacturing company with efficient workflows remains competitive in the marketplace because it is more productive than its competitors. Digital manufacturing workflows also enhance inventory management, ensuring a business runs optimally.
A company can optimize its manufacturing workflows—improving, simplifying, and scaling processes that work. Optimizing entire processes means that manufacturing is more effective and lucrative. Human workers have more time to fine-tune processes and focus more on tasks that can’t be automated.
In industry 5.0, humans work alongside machines to create more effective, future-proof processes. Digital workflows help manufacturers use the least resources to obtain the highest profits. Man and machine work together for the best financial outcome for their organizations. Optimize your manufacturing workflows for Industry 5.0 with Kissflow for workflow automation.
Manufacturing workflow management means organizing and coordinating manufacturing tasks that produce a specific outcome. It ensures workflows are optimized, improved, and automated wherever possible to eliminate repetition, increase output, and reduce errors.
A manufacturing workflow can include several steps and involve a combination of systems, people, or machines. People managing workflows should constantly search for opportunities to eliminate bottlenecks and improve visibility into the flow. You can automate the processes in your manufacturing company, streamline them, and improve workflows to boost productivity.
Here are the top 3 challenges in improving manufacturing workflows:
Using the Wrong Technology Solution
Poor Workflow Mapping
Invisible Bottlenecks
The wrong technology solution can slow down manufacturing workflows. Choosing the solution that effectively solves bottlenecks in workflows is crucial. Some manufacturing companies make the mistake of using sophisticated technology to solve problems without first understanding why processes are failing.
Industry 5.0 promotes robots and smart machines to help humans work better and faster by using advanced technologies like big data and the Internet of Things (IoT). Technology’s main job is to amplify human effort and processes. If the processes are bad, it will only make the situation worse. Before a company gets manufacturing workflow software, it should first understand workflow bottlenecks, the areas of improvement, pre-set ROI, etc.
To truly maximize the efficiency of workflows, the manufacturing company must identify the processes that contribute to the workflows and eliminate bottlenecks that could hinder them from succeeding. Manufacturing companies have multiple workflows running at any given time, but most of them are undefined or unmapped.
Undefined workflows often develop out of need and aren’t truly efficient. Over time, they become part of the work culture and are hard to eliminate. In many cases, workflows are undefined because it’s time-consuming to identify bottlenecks.
Mapping workflows takes time, but it can greatly improve the health of the organization. Workflow maps document processes and provide a reference point and an overview of how things should be done. You can analyze the process steps and identify those that can be automated, which ones need to be cut out, and the blockage that slows down production. If you don’t map your workflows, you'll end up getting the wrong technology solution that is only going to cause further congestion.
Identifying bottlenecks is the key to improving workflows for manufacturing companies. Bottlenecks that are easily overlooked or too small can create huge problems later on. Ignored bottlenecks can become almost invisible but create weak links in workflows.
To improve workflows, find out how many bottlenecks you have and where they originate. Performing a workflow audit can bring new information to processes. This new information can shed light on problems that might remain the same over time. You must actively look for bottlenecks to find them because some are more elusive than others.
In most manufacturing plants, production processes comprise steps that lead to the final product coming off the line. But these processes take time to get completed, especially the manual ones. To be more productive, manufacturers must automate operator workflows to ensure that steps are completed quickly and consistently without quality defects.
Manufacturing process automation eliminates repetitive, menial tasks, allowing employees to focus on aspects of the production process that require more human intervention. Additionally, digitized workflows enable businesses to automate data collection across multiple channels. They can track production more efficiently and receive real-time feedback on any issues that may arise. Industry 5.0 prioritizes human needs over the production process, so manufacturers must get solutions that allow workers to be more productive and agile.
Manual processes present many challenges related to data security and integrity. They are also susceptible to human error and can be incredibly inaccurate. For instance, production data recorded on paper can be difficult to sort, refer to, and analyze.
Industry 5.0 enables sustainable manufacturing supported by technologies that efficiently use resources. Digital workflows help make it a reality by allowing manufacturing plants to streamline data collection for sustainable manufacturing. Supervisors can easily analyze and respond to production data in real-time and make informed decisions.
Manufacturers that embrace Industry 5.0 become more competitive because they cut manufacturing costs. Most manufacturing processes contain inefficiencies that can significantly increase unnecessary production costs and reduce productivity. For example, if quality control is done manually, a manufacturer may lose money due to rejects and damaged items. Digital workflows allow quality control personnel to easily track defective items, ensuring no costs are incurred due to non-compliance or material wastage.
Industry 5.0 empowers workers by putting them at the center of industry. Empowered workers are more productive as they can easily up-skill and re-skill. Forward-thinking manufacturers eliminate information silos that make real-time production visibility difficult. Departments collaborate, ensuring no time is wasted putting together different information originating from various departments.
Digital workflows also allow for more convenient information sharing. Employees can execute their tasks efficiently because they don’t have to collect paperwork from various departments or locations.
Cross-trained employees are adaptable. They can quickly adapt to changing production schedules and unexpected events.
To consistently improve your workflows, set, establish and monitor the key metrics that drive the business in real-time.
This ensures a single item is completed for every item started. Products are manufactured with as little “in-between work” as possible.
Manufacturing processes can only be improved with manufacturing workflow software. The right software can manage projects at every stage.
Digital supply chains offer more visibility. Manufacturers can identify issues that may disrupt processes and quickly address them. Digital workflows are also customer-focused, so companies gain more understanding of customer needs and what to do to improve customer experiences.
Digital workflows provide real-time, holistic information about requirements, performance, and status. Decision-makers can use this information to optimize processes such as operational logistics, raw material flows, and inventory levels. Improved collaboration also helps manufacturers identify process bottlenecks, accelerate innovation, reduce time-to-market, and boost innovation ROI.
Automated workflows eliminate paper-based, manual supply chain processes. All the required information is readily available to whoever needs it. They also bring about manufacturing process automation, improving process efficiency, worker productivity, and profitability. Ultimately, connectivity enables a manufacturing plant to optimize its supply chain and redefine new business strategies.
Because a digital supply chain is enabled by many data-driven technologies, a manufacturer can connect data sources to improve preventive maintenance and inventory management. Data can be used to identify inefficiencies, enhance product quality, and improve customer experiences.
Digital workflows provide updated quality and control data, ensuring a company anticipates issues and responds fast. A digital supply chain also makes it easier to plan and manage supply chain workflows, procurement, inventory management, and logistics management.
Learn more about logistics management software.
Digital workflows allow manufacturers to enhance operations and satisfy customer needs. By using digital tools and technologies, they can collaborate with vendors, third-party service providers, and customers to improve the performance of the end-to-end value chain.
Try Kissflow's workflow software, a comprehensive, unified digital work platform that addresses labor shortages, poor inventory management, low sales, and day-to-day inefficiencies.
Related Articles
Welcome.
Let's get started.
To begin, tell us a bit about yourself
By proceeding, you agree to our Terms of Service and Privacy Policy
"The beauty of Kissflow is how quick and easy it is to create the apps I need. It's so user-friendly that I made exactly what I needed in 30 minutes."
Oliver Umehara
IT Manager - SoftBank
A Trusted Choice for Companies Globally
Thank you for signing up
Someone from our team will contact you soon.
Know why all the IT leaders converging at booth #602
Earn a chance to be part of our experience event
Get the first look at the 2024 Citizen Development report
Welcome.
Let's get started.
By proceeding, you agree to our Terms of Service and Privacy Policy
Wondering where to start?
Let's talk!
Connect with our solution experts to gain insights on how Kissflow can help you transform ideas into reality and accelerate digital transformation
This website uses cookies to ensure you get the best experience. Check our Privacy Policy