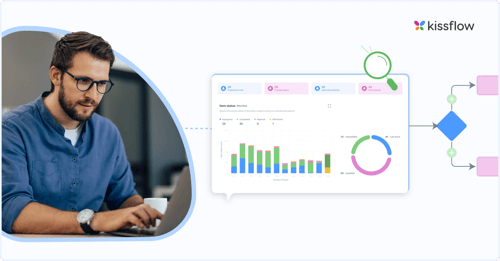
- >
- Solutions>
- Manufacturing>
- Optimizing Manufacturing Workflows with Automated Product Tracking
Optimizing Manufacturing Workflows with Automated Product Tracking
Team Kissflow
Updated on 16 Apr 2025 • 7 min read
Accurate, end-to-end product tracking has become essential in manufacturing. As speed, cost efficiency, and quality demands rise, manual tracking systems struggle to keep pace with high-speed production environments. Workflow automation addresses these challenges by enabling real-time, precise visibility at every production stage. By automating formerly manual tasks, manufacturers can reduce errors, ensure accuracy, and save valuable time.
Workflow automation goes beyond simple tracking. Through tools like RFID, IoT sensors, and barcode scanning, manufacturers can oversee product movement and inventory with unprecedented control. Real-time data allows managers to address issues, keeping production efficient and on target quickly. For manufacturers, adopting automation is essential for maintaining pace, gaining a competitive edge, and meeting the high standards of today’s industry.
What is automated product tracking in manufacturing?
Automated product tracking is a technology-driven approach that enables manufacturers to monitor the movement and status of products in real-time throughout the production process. Leveraging advanced tools like RFID (Radio Frequency Identification) tags, barcode scanning systems, and IoT (Internet of Things) sensors, automated tracking provides continuous, real-time updates on product location, status, and inventory levels. This end-to-end visibility allows manufacturers to track every phase of a product’s journey, from sourcing raw materials to the final shipment stages.
RFID tags and IoT sensors are often embedded directly into products or production equipment in an automated system. This setup enables constant data collection, which integrates seamlessly with centralized software. Unlike manual tracking, where data entry and physical checks can slow down processes and introduce errors, automated monitoring ensures that each update is precise and instantaneous. This automation gives manufacturers the confidence that their inventory data is always current and accurate, enabling proactive decision-making and better resource management across production lines.
Challenges of manual product tracking without automation
Without automation, manual product tracking presents several challenges that can disrupt production efficiency and lead to costly errors. Here are the primary issues manufacturers face with manual tracking:
-
Human errors: Manual entry is prone to mistakes, especially in large-scale manufacturing. Missed scans, input errors, or misplaced items can throw off entire inventories and delay production.
-
Lack of real-time data: Manual tracking cannot deliver instant updates on product status. Delayed information creates a lag between a product’s actual location and its recorded location, making it difficult for managers to respond promptly to issues, causing bottlenecks.
-
Operational inefficiencies: Manual tracking demands frequent hands-on checks and data entry, consuming valuable time and resources. This approach slows production cycles significantly when teams frequently update products or coordinate across multiple departments.
-
Production and cost risks: Inefficient tracking increases the risk of lost or misplaced items, inaccurate inventories, and shipment errors, significantly costing the manufacturing process. For example, delayed shipments due to incorrect inventory counts can impact customer satisfaction and the company’s bottom line.
Areas of automation in the manufacturing industry
In manufacturing, workflow automation streamlines and transforms processes. By implementing automation across critical areas like inventory, quality control, order processing, and logistics, manufacturers can unlock new efficiency, accuracy, and power levels. Let’s explore how each of these areas benefits from automation.
1. Inventory management
Managing inventory is essential in manufacturing, where shortages or excess stock can lead to significant inefficiencies and increased costs. Workflow automation allows manufacturers to monitor inventory levels in real-time, automatically updating stock counts as products move through production. Automated tracking lets stakeholders see current inventory levels, enabling more precise forecasting and better-informed procurement decisions. Automation also supports just-in-time inventory practices, reducing the need for excess stock and helping manufacturers avoid costly overproduction.
2. Quality control
Ensuring consistent product quality is crucial in maintaining brand reputation and meeting customer expectations. Automated quality control systems monitor each production stage, capturing data on critical quality parameters. These systems can detect deviations in real-time, flagging issues the moment they occur and enabling quick corrective action. Automated quality control helps minimize production delays caused by quality-related matters and reduces the need for extensive post-production inspections. This proactive approach ensures that every product meets quality standards before it moves to the next stage, ultimately decreasing waste and improving customer satisfaction.
3. Order processing and fulfillment
Order processing and fulfillment often involve multiple steps, from validating orders to packaging and shipping. Automating these steps simplifies the movement of products through the supply chain. With automated order validation, manufacturers can quickly confirm orders, reducing the chance of errors. Packaging and shipping processes can also be automated, speeding up fulfillment times and ensuring products reach customers faster. By keeping the entire order flow automated, manufacturers can maintain a consistent level of service, enhance customer satisfaction, and streamline supply chain operations.
4. Logistics and shipping
Logistics and shipping are critical to delivering finished products accurately and on time. Automated tracking systems make it easy for manufacturers to monitor shipments from production to delivery, providing real-time visibility into every stage of transit. With workflow automation, logistics managers can quickly address potential delays, track product location, and reduce the risk of misplaced items. Automated tracking also allows manufacturers to share real-time updates with customers, enhancing transparency and building trust. By maintaining control over logistics, manufacturers can reduce shipping errors, delivery times, and overall efficiency in getting products to their destinations.
Learn more about logistics management software.
Why do automating these functions matter?
Workflow automation across these areas isn’t just a matter of convenience; it drives tangible results. Automated inventory systems prevent costly stock issues, while real-time quality control ensures that products meet standards without holding up production. Automated order processing and logistics enhance speed and reliability across the supply chain, keeping customers happy and operations running smoothly. Together, these areas of automation give manufacturers a robust, interconnected system that supports higher productivity, reduced costs, and a competitive edge in a demanding market.
Benefits of automating processes
Automation in manufacturing offers essential advantages, enhancing efficiency, accuracy, and compliance. Here’s a closer look at the most impactful benefits.
1. Reduced workload and operational costs
Automating repetitive, manual tasks saves time and resources, allowing manufacturers to focus on more complex, high-value work. Automation minimizes labor-intensive processes by reducing the need for manual data entry and hands-on checks, lowering costs, and eliminating inefficiencies. Teams can allocate resources more effectively, streamline workflows, and maximize productivity.
2. Improved accuracy and traceability
Manual tracking often leads to errors, from data entry mistakes to inventory miscounts, resulting in production disruptions and costly discrepancies. Automation precisely captures data at each production stage, using technologies like RFID, IoT sensors, and barcode scanning. The system tracks every product accurately, creating a transparent and traceable record from production through delivery. This accuracy strengthens quality control, enabling managers to quickly identify and resolve issues and reducing the risk of defective products reaching customers.
3. Enhanced compliance with industry regulations
Regulatory compliance is crucial in manufacturing, where even minor lapses can result in penalties or costly recalls. Automation strengthens compliance by generating real-time audit trails at each production stage, logging every movement or status update to create a continuous, verifiable record. This process helps manufacturers stay compliant and ensures accountability during audits. Furthermore, automation provides rapid access to compliance data, allowing manufacturers to respond promptly to regulatory inquiries.
4. Faster decision-making with real-time data and insights
Automation provides immediate access to real-time data, giving stakeholders an up-to-the-minute view of production status, inventory levels, and potential issues. This level of insight allows for swift, informed decisions, reducing downtime and improving agility. For example, managers can assess stock levels in a supply chain disruption and adjust plans accordingly. With accurate, real-time data, manufacturers stay adaptable and responsive to shifts in demand, production challenges, or market fluctuations.
Why is automation essential?
The combined benefits of reduced workload, improved accuracy, regulatory compliance, and agile decision-making highlight the critical role of automation in manufacturing. Manufacturers can optimize production cycles, reduce costs, and deliver consistently high-quality products by automating core processes. Automation equips companies to meet competitive demands and prepares them for sustainable growth and resilience in the future.
Key features every product tracking automation tool should have
For a product tracking automation tool to excel in a manufacturing setting, it needs features that ensure accurate, real-time tracking and drive operational efficiency. Here are the essential features that make these tools indispensable for manufacturers aiming to improve product tracking.
1. Real-time monitoring and alerts
Manufacturing requires immediate awareness of any issues or changes in production. Real-time monitoring allows manufacturers to track products at each stage, ensuring that disruptions are immediately visible. Alerts notify key personnel when an issue arises, whether a delay, inventory shortage, or equipment malfunction, enabling rapid responses to prevent downtime and minimize losses. This instant visibility is essential for maintaining smooth operations and allows manufacturers to address issues before they escalate.
2. Customizable dashboards
Every manufacturing facility has unique goals and key performance indicators (KPIs), so customizable dashboards are critical. Dashboards let users select and track KPIs most relevant to their specific manufacturing goals, such as production speed, inventory status, and defect rates. With a tailored view, decision-makers can gain insights into real-time and historical data, helping them identify patterns and optimize production processes. Customizable dashboards empower managers to monitor metrics that matter most to their operation and adjust strategies based on the data.
3. Easy integration with ERP, SCM, and core systems
Product tracking automation tools need uninterrupted integration with systems like ERP (Enterprise Resource Planning) and SCM (Supply Chain Management) for practical functionality. Such integration ensures a consistent flow of information across departments, from procurement to production and logistics. Unified data from these systems allows manufacturers to maintain accurate inventory levels, streamline workflows, and eliminate data silos that can create inefficiencies. This connectivity also enhances insights, empowering manufacturers to make data-driven decisions with a comprehensive view of operations.
4. Scalable architecture to support growth
Manufacturing demands often scale up or down based on market conditions, so a robust automation tool should support this flexibility. The scalable architecture ensures the tool can handle increased production volume, additional users, and expanded tracking needs without compromising performance. As manufacturing facilities grow or diversify, the automation tool should seamlessly accommodate the increased demands. This scalability allows manufacturers to invest in long-term automation investments without worrying about outgrowing the tool.
5. User-friendly interface for both technical and non-technical users
An intuitive, user-friendly interface ensures that team members at all technical levels can efficiently use the tool. For product tracking automation to be effective, it must be accessible to everyone involved, from factory floor operators to data analysts and senior managers. A well-designed interface minimizes the need for extensive training, encourages adoption across the organization, and helps teams use the tool to its fullest potential. When everyone navigates the system confidently, they are more likely to maintain accurate tracking and maximize the benefits of automation.
Why these features matter
These essential features, real-time monitoring, customizable dashboards, seamless integration, scalability, and user-friendly interfaces combine to create a powerful tool for modern manufacturing. Real-time alerts and monitoring provide agility, while customizable dashboards and integration with core systems ensure data consistency and actionable insights. Scalability allows manufacturers to grow without interruption, and a user-friendly design promotes widespread adoption. These features equip manufacturers to handle complex production demands, reduce inefficiencies, and drive continuous improvement. For CIOs and product managers, investing in automation tools with these capabilities is a strategic move that aligns with operational goals and long-term growth strategies.
How can Kissflow help your manufacturing business?
Kissflow’s workflow automation platform offers manufacturers an effective way to enhance product tracking with minimal manual effort. As a low-code solution, it provides flexibility to adapt workflows, ensuring real-time monitoring across every production stage. Enabling manufacturers to maintain precise visibility from start to finish, reduce errors, and meet regulatory standards, all while streamlining core tracking tasks and minimizing manual interventions.
Kissflow centralizes data and insights, enabling informed, timely decision-making that keeps production efficient and compliant. Manufacturers can tackle common challenges like data silos and tracking inconsistencies while gaining complete traceability over operations. Kissflow’s automation capabilities prepare them to meet industry demands, optimize resource allocation, and achieve long-term operational efficiency.
For more details on elevating your manufacturing operations, visit Kissflow’s Manufacturing page.
Related Articles
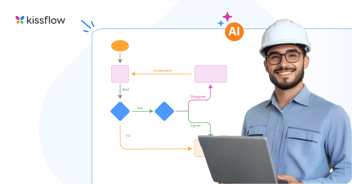
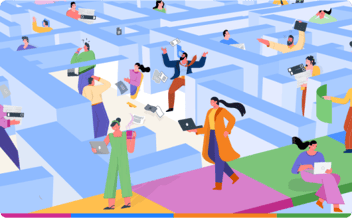
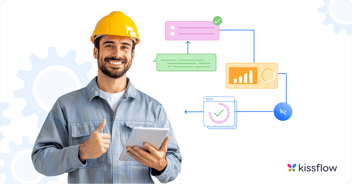