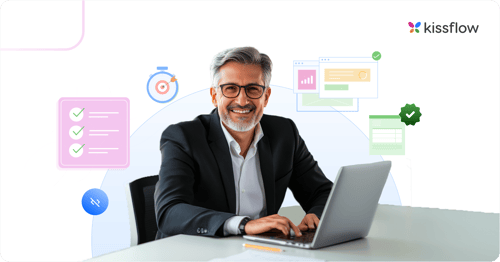
- >
- Oil & Gas>
- How Modern Solutions Drive Pipeline Downtime Reduction and Safety Excellence
How Modern Solutions Drive Pipeline Downtime Reduction and Safety Excellence
Team Kissflow
Updated on 21 Jul 2025 • 6 min read
Pipeline downtime costs the oil and gas industry billions every year. A single incident can shut down operations for days, trigger regulatory investigations, and damage a company's reputation for years. Yet most companies still rely on paper-based inspections, manual reporting systems, and fragmented communication channels that practically guarantee problems will slip through the cracks.
You know this reality if you're a CTO, CIO, or operations leader in oil and gas. Your teams do their best with outdated tools, but good intentions can't prevent the inevitable: critical issues get missed, reports get delayed, and small problems become expensive disasters.
The solution isn't another massive IT overhaul or lengthy ERP implementation. It's building a digital operations backbone that connects your people, processes, and data without disrupting the systems that already work. Modern platforms can accelerate development processes, reducing the time required to build applications by up to 90 percent[1] compared to traditional methods. This rapid deployment capability is crucial for pipeline downtime reduction, where minimizing interruptions directly impacts productivity and safety.
In this post, we'll discuss how digital solutions can transform your pipeline integrity management operations, enable comprehensive oil and gas safety automation, and give you the real-time visibility that traditional systems simply can't deliver. We'll also show you exactly how other companies are making this work without massive IT overhauls.
The operational cost of pipeline disruptions
Let's talk numbers. When pipeline downtime reduction isn't properly managed, you're not just looking at repair costs. You're dealing with lost production that can reach millions per day, regulatory fines that keep climbing, and the kind of reputational damage that takes years to repair.
But here's what makes this tricky: unplanned downtime doesn't just cost money. It creates safety risks. When teams rush to fix problems, shortcuts happen. When communication breaks down during emergencies, people make mistakes. And when you can't see what's happening across your entire pipeline network, small issues become big disasters.
Think about managing field inspections across thousands of miles of infrastructure. Your teams are spread across different time zones, using different forms, and reporting through different channels. One inspector might catch a minor leak and write it on paper. Another might spot corrosion but forget to include the GPS coordinates. A third might take photos but can't upload them until they return to the office.
Meanwhile, that minor leak becomes a major rupture because the report sat in someone's inbox for three days.
This fragmented approach doesn't just slow things down. It creates blind spots. When incident reporting takes too long, when documentation gets lost, and when response workflows move at a snail's pace, you're essentially playing Russian roulette with your pipeline integrity management.
Building your digital operations backbone with automated field inspections
Here's where things get interesting. A digital operations backbone lets your teams create standardized digital processes that work right on their phones or tablets. No more paper safety checklists that get soggy in the rain or illegible handwriting that nobody can decode.
Imagine your field inspector pulling up a digital checklist specifically designed for that section of pipeline. They can record pressure readings with dropdown menus, snap photos of potential issues, and even use GPS to automatically tag the exact location. If they spot something outside normal parameters, the system flags it immediately, with no waiting or guessing.
Let's say Sarah's doing a routine inspection at Station 12. She notices some unusual corrosion patterns and takes a photo. The inspection app she's using doesn't just store that photo. It timestamps it, adds GPS coordinates, and compares the corrosion level against predefined thresholds. If it crosses a critical point, the system sends an alert to the maintenance team before Sarah finishes her inspection.
The best part? You can set up recurring field inspections that automatically assign tasks based on pipeline risk levels, regulatory requirements, or seasonal factors. No more manual scheduling, no more forgotten inspections, no more hoping everyone remembers their assignments.
These oil and gas safety automation systems also boost your operational efficiency by creating standardized processes that every inspector follows, regardless of their experience level or location. When integrated with tools like a ROW Violation Tracker, your teams can immediately identify and respond to right-of-way encroachments that could threaten pipeline integrity.
Safety incident reporting and resolution workflows that actually work
Quick question: How long does it take for a safety incident report to reach the right person in your organization? If the answer is "too long" or "I'm not sure," you've got a problem that's affecting your pipeline downtime reduction efforts.
Your digital operations backbone changes this completely. Any field worker can report a safety incident instantly using a simple mobile app. Leak detected? Tap, type, submit. Environmental concern? Photo, description, send. Equipment malfunction? Record, categorize, escalate.
But here's the real magic: these incident reporting systems don't just disappear into the void. They trigger automatic workflows based on your operational procedures. A minor leak might notify the local maintenance team. A major spill could alert the emergency response team, regulatory contacts, and senior management simultaneously.
Let's walk through a scenario. Jake, a pipeline technician, notices what looks like a small gas leak during his morning rounds. Using his company's incident reporting app, he snaps a photo, selects "Gas Leak - Minor" from a dropdown, and adds a quick voice note about the smell intensity.
The moment he hits submit, the system springs into action. The local repair crew gets notified and dispatched. The safety manager receives an alert with Jake's exact location and photo evidence. The incident gets logged with a unique tracking number that follows it through investigation, repair, and final resolution.
No phone tag. No lost paperwork. No wondering if the right people know about the problem.
This workflow automation approach improves operational efficiency by eliminating communication gaps that traditionally slow down response times. When combined with a Pipeline Repair Work Permit workflow, your teams can ensure that all safety protocols are followed while minimizing downtime during repairs.
Real-time visibility and audit readiness through pipeline integrity management
Remember that feeling of flying blind when executives ask about pipeline status? Those days are over with proper real-time visibility systems built into your digital operations backbone.
Modern platforms can create dashboards showing exactly what's happening across your entire pipeline network. Open safety issues, overdue field inspections, maintenance backlogs, high-risk areas. All visible at a glance.
Imagine logging into your system and seeing a map with color-coded pipeline segments. Green means everything's running smoothly. Yellow indicates scheduled maintenance is coming up. Red flags urgent attention is needed. You can drill down to see specific incidents, track repair progress, and identify patterns before they become problems.
This level of pipeline integrity management visibility gives you unprecedented control over your operations. You can see trends in corrosion rates, identify recurring problem areas, and proactively schedule maintenance before issues become critical.
When audit readiness time comes around? Every action in your digital applications gets logged automatically. Who reported what, when they reported it, what actions were taken, and how long everything took. Regulators love this kind of detailed documentation because it shows you're not just compliant. You're proactive.
Export reports with a few clicks. Generate compliance summaries in minutes instead of days. Show auditors a complete chain of custody for every incident from initial report to final resolution.
This level of real-time visibility improves your operational efficiency by helping you spot trends and allocate resources where they're needed most. Your oil and gas safety automation programs become data-driven instead of reactive.
Practical implementation: From field operations to executive oversight
Here's something that might surprise you: the most successful digital transformation initiatives don't disrupt operations. They enhance them by giving field teams exactly what they need while providing management with the visibility they've always wanted.
Your maintenance managers and process owners can work with IT to build exactly the workflows they need without waiting months for custom development. They understand the day-to-day challenges better than anyone, so the solutions actually work in the field.
But governance stays where it belongs. Access permissions, data security, and integration with your existing ERP and maintenance systems all remain under IT control. It's about empowering your operations teams while maintaining the oversight and control necessary for managing critical infrastructure.
This approach works because solutions get built by the people who actually use them. Your safety checklists reflect real field conditions. Your incident reporting workflows match how emergencies actually unfold. Your audit readiness processes capture the data regulators actually want to see.
Whether you're implementing a ROW Violation Tracker to monitor pipeline easements or setting up a Pipeline Repair Work Permit workflow to streamline maintenance approvals, your teams can deploy these solutions quickly and see immediate results.
Making pipeline downtime reduction a reality
Pipeline downtime reduction isn't just about having better technology. It's about connecting your people, processes, and data in ways that prevent problems before they start.
Building your digital operations backbone gives you that connection without the complexity.
Your field teams get tools that actually help them do their jobs better. Your managers get real-time visibility into what's really happening. Your IT team gets to focus on strategic initiatives instead of managing disconnected spreadsheets and email chains.
The companies seeing the biggest wins in pipeline integrity management are the ones that start small and scale up. They pick one pain point (maybe incident reporting or field inspection scheduling) and solve it well. Then they expand to other areas once they see the results.
Your pipelines are critical infrastructure. The systems managing them should be just as reliable, flexible, and ready for whatever comes next. That's exactly what a modern digital operations backbone delivers, and why more oil and gas companies are transforming their operations every day.
When you combine automated safety checklists, streamlined incident reporting, enhanced audit readiness, and improved operational efficiency through oil and gas safety automation, you get comprehensive pipeline integrity management that works in the real world.
Ready to see how digital solutions can transform your pipeline operations and build your digital operations backbone?
Related Articles