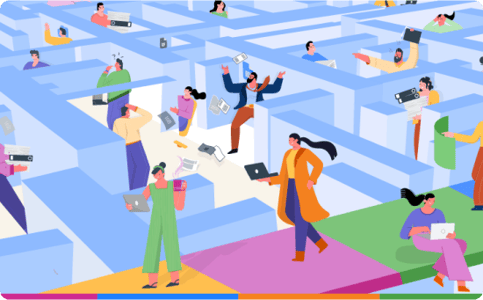
- >
- Solutions >
- Top 3 Challenges of IT in Manufacturing Industry and How to Solve Them
Top 3 Challenges of IT in Manufacturing Industry and How to Solve Them
Team Kissflow
Updated on 13 Jun 2025 • 7 min read
The manufacturing industry remains a key cornerstone of economies worldwide, driving innovation, creating new opportunities, and fostering economic growth. Over the years, this vital sector has witnessed a remarkable transformation, primarily fueled by advancements in information technology.
Today, players in the manufacturing industry are embracing automation and adopting intelligent systems that can potentially optimize operations, and help them deliver high-quality products to the market.
This shift towards a digitalized and interconnected manufacturing ecosystem is often referred to as Industry 4.0 or the Fourth Industrial Revolution. But while such changes ushers in a host of new opportunities, it also creates new challenges for companies operating in the sector.
IT is at the core of transformation in the manufacturing industry
The rapid integration of Information Technology (IT) has emerged as a defining characteristic of today's manufacturing landscape. IT lies at the core of rapid digitalization, automation, and increased connectivity that is changing how traditional manufacturing industries operate. It is also driving innovation and revolutionizing internal and external collaboration within the manufacturing industry.
One of the key aspects of this ongoing transformation is the ability to collect, analyze, and utilize vast amounts of data throughout the manufacturing value chain. By deploying new technology in the form of sensors, embedded systems, and IoT devices that power essential manufacturing processes, manufacturers can collect real-time data that provides invaluable insights into their production processes and supply chain dynamics.
IT is powering the seamless integration and interoperability of various components within the manufacturing ecosystem. Through the use of interconnected systems and standardized protocols, manufacturers can achieve end-to-end visibility and control over their operations.
For instance, the use of Enterprise Resource Planning (ERP) systems that streamline production planning and Supervisory Control and Data Acquisition (SCADA) systems that monitor and control industrial processes help manufacturing companies maintain a smooth flow of information.
Automation is another way IT is transforming the manufacturing industry. Robotic process automation (RPA), machine vision, and collaborative robots (cobots) are being increasingly deployed in manufacturing plants and warehouses. These automation tools replace manual labor with faster, more precise, and more consistent processes.
Automation apps built on basic IT systems and algorithms are also helping manufacturing companies perform day-to-day office operations like employee management, inventory allocation, invoicing, and documentation more effectively. By automating these repetitive processes, manufacturers can achieve higher productivity, reduce costs, and improve the overall efficiency of their internal processes.
The current state of IT and the cause of declining performance
As more companies in the manufacturing industry adopt IT systems and solutions, remarkable changes are being seen in the areas of efficiency, productivity, and innovation. Despite its many potential benefits, the current state of IT in the manufacturing sector is not without challenges.
Aside from economic and market-related pressures such as inflation and changing consumer behavior, manufacturers continue to face operational challenges that may limit the adoption of digital technology and stifle results.
Several factors contribute to declining IT performance, hindering manufacturers from fully realizing the advantages offered by technology. Many manufacturing companies still operate with outdated legacy systems that lack the flexibility, scalability, and integration capabilities required to meet the demands of current IT-powered manufacturing practices.
Lack of interoperability is another reason for declining IT adoption. As in every industry, manufacturing environments are designed in a way that requires various systems and equipment to communicate seamlessly to optimize operations. However, interoperability challenges arise when different IT systems do not integrate smoothly. This lack of interoperability hampers data sharing, collaboration, and the implementation of end-to-end solutions that foster digital change in manufacturing.
Then there’s the skills gap caused by the evolving nature of IT in the manufacturing sector. To keep up, manufacturing companies need a skilled workforce that can effectively build and manage new technology. The shortage of professionals proficient in the key areas of IT for manufacturing is a burden that’s stifling performance.
Top three challenges of IT for the manufacturing industry
Despite the growth momentum being experienced by manufacturers in the area of IT, there are lingering challenges that threaten the movement. These challenges not only make adopting new IT difficult, they could also potentially stall digital transformation for manufacturing companies unless innovative solutions are adopted.
1. Data management and analytics
One of the consequences of adopting machines, sensors, and supply chain systems that facilitate efficiency in manufacturing processes is the vast amounts of data they generate.
Managing, analyzing, and utilizing this data effectively poses significant challenges to manufacturers.
To ensure data quality, accessibility, and data integrity, manufacturers need robust data management practices. There’s also a need for advanced analytics systems that can help derive actionable insights needed to optimize processes, forecast intelligently, take predictive actions, and improve overall decision-making.
How to solve them
Deploying appropriate data governance frameworks and leveraging data analytics tools and platforms are some of the key strategies that can help overcome this challenge. App development platforms often provide the frameworks and tools needed to achieve such efficient data management and analytics integration.
Modern app development platforms offer capabilities that allow users to connect and integrate with various data sources to achieve seamless data flow between applications and backend systems. By leveraging these features, manufacturers can streamline their data management processes and derive valuable insights to power decision-making.
2. Integration and interoperability
Manufacturing operations are complex. They require a wide range of systems, equipment, and software applications that need to work seamlessly together. Achieving integration and interoperability is even more difficult when you try to combine modern IT solutions with legacy systems not built to integrate with such complex components.
Incompatibility between legacy systems and modern technologies, or even between modern systems with varying data formats, and differing communication protocols hinders the smooth information flow and collaboration across the manufacturing value chain.
How to solve them
Implementing standardization protocols, adopting open architectures, and leveraging technologies such as application programming interfaces (APIs) and middleware are some of the strategies manufacturers can adopt to address integration and interoperability challenges.
Instead of relying on legacy ERPs that are often too complex to manage and difficult to alter, a low-code app development platform can be used to implement digital change in manufacturing processes.
App development platforms often support integrations with existing systems and provide tools for seamless data exchange and communication. These platforms may offer APIs, connectors, and middleware that facilitate integration with legacy systems, modern applications, and external services.
By using an app development platform with robust integration capabilities like Kissflow, manufacturers can overcome interoperability challenges, integrate disparate systems, and establish efficient communication within their IT ecosystem.
3. Skill gap and workforce readiness
One of the consequences of the rapid advancement of IT in the manufacturing industry is a growing skill gap that’s difficult to keep up with. There is a shortage of professionals with expertise in key areas such as data analytics, cybersecurity, cloud computing, artificial intelligence, and robotics, especially when it comes to the manufacturing industry.
As a result, manufacturers face challenges in finding and retaining skilled IT personnel who can effectively manage and leverage technology within the manufacturing context. Additionally, there is a need to upskill and reskill the existing workforce to adapt to technological changes and embrace digital transformation.
How to solve them
Bridging the skill gap and ensuring workforce readiness is crucial for successful IT implementation and utilization in the manufacturing industry. Modern app development platform often provides intuitive and low-code or no-code development environments for implementing digital solutions.
These platforms remove the complexities of traditional software development, allowing even business users or individuals with limited coding experience to build apps needed to drive the desired innovation.
By leveraging a low-code app development platform, manufacturers can empower their existing workforce to participate in application development initiatives, reducing the skill gap and fostering workforce readiness for utilizing IT tools and platforms for manufacturing.
Benefits of strengthening IT and adopting quicker app development solutions in manufacturing
Utilizing an app development platform provides manufacturers with a comprehensive set of tools, frameworks, and features that address key IT challenges while achieving additional benefits.
Some of the benefits of strengthening IT and adopting quicker app development solutions in manufacturing include:
1. Enhanced operational efficiency
Apps can be developed to optimize production planning, scheduling, inventory management, and supply chain logistics. Strengthening IT can also help manufacturers automate manual tasks, monitor data in real-time, and achieve process optimization that can significantly improve overall operational efficiency.
Learn more about logistics management software.
2. Agile decision-making
With faster access to accurate and actionable information, decision-makers can make informed decisions promptly, identify bottlenecks or inefficiencies, and proactively address issues to drive continuous improvement.
3. Enhanced collaboration and communication
App development solutions provide centralized platforms for sharing information, coordinating activities, and managing workflows. By enabling seamless communication and collaboration among employees, departments, suppliers, and partners, manufacturers can foster better teamwork, reduce errors, and improve overall operational effectiveness.
4. Flexibility and scalability
Enterprise app development platforms often offer cloud-based solutions that provide scalability, flexibility, and cost-effectiveness. Manufacturers can scale their applications and infrastructure based on business needs, giving them the ability to handle increased data volumes, user demands, or expanding operations.
Conclusion
Despite the challenges of implementing IT for manufacturing businesses, failing to embrace innovation is even more costly. This is why manufacturers should invest in innovative solutions that can strengthen their IT implementation and foster a culture of innovation within their organization. Manufacturers that succeed at achieving this are able to gain a competitive advantage in a rapidly evolving industry.
Get started with the Kissflow Platform and learn how to leverage its features to drive better results
Frequently Asked Questions:
1. What are the biggest IT challenges in manufacturing?
Biggest IT challenges in manufacturing include integrating legacy operational technology with modern IT systems, ensuring cybersecurity without disrupting production, maintaining system availability for 24/7 operations, managing data from IoT devices and sensors, implementing industry-specific compliance requirements, supporting remote locations with limited connectivity, and balancing innovation with stability requirements.
2. How does AI help overcome IT issues in manufacturing?
AI helps overcome IT issues in manufacturing by predicting equipment failures before they cause downtime, optimizing production scheduling based on multiple variables, automating quality inspection through computer vision, providing real-time analytics for process optimization, enabling natural language interfaces for shop floor systems, enhancing cybersecurity through anomaly detection, and bridging the gap between operational technology and information technology systems.
3. What are best practices for managing IT infrastructure in factories?
Best practices for managing IT infrastructure in factories include implementing OT/IT convergence strategies with appropriate security controls, designing for high availability with redundant systems, adopting edge computing for latency-sensitive applications, implementing comprehensive backup and disaster recovery, developing specialized IoT management capabilities, creating strict change management procedures, and implementing predictive maintenance for critical systems.
4. How can manufacturers optimize their IT operations?
Manufacturers optimize IT operations by implementing edge computing reducing latency for production systems, adopting industrial IoT platforms for equipment monitoring, implementing specialized MES (Manufacturing Execution Systems) integrated with enterprise systems, developing comprehensive OT/IT security strategies, creating digital twins for virtual testing, implementing predictive maintenance reducing downtime, and developing specialized disaster recovery plans for production environments.
5. What cybersecurity risks do manufacturing IT teams face?
Cybersecurity risks manufacturing IT teams face include operational technology vulnerabilities in legacy equipment, increased attack surface from connected IoT devices, potential for production disruption from ransomware, challenges implementing patches without downtime, intellectual property theft targeting proprietary designs, supply chain security vulnerabilities, difficulty segmenting networks while maintaining operations, and shortage of specialized industrial cybersecurity skills.
"The application is very dynamic and useful in all our business cases and the platform is very user-friendly and implementation was great."
Thanks for submitting.
Our solution experts will connect with you to get started.
Related Articles
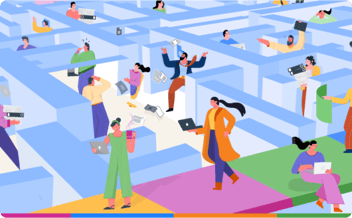