A customer places an order at 2 PM on Tuesday. By Thursday morning, that product sits on their doorstep. The process appears seamless to the end user.
Behind this simple transaction lies a web of coordination that would make most executives pause. Suppliers, warehouses, transportation networks, and tracking systems must all function in perfect harmony. For technology leaders, this coordination represents both opportunity and challenge.
Most organizations struggle with logistics and supply chain management because they treat these functions as separate entities. The results speak for themselves: Delays compound, costs escalate, and customer satisfaction suffers.
The market data reinforces this urgency. The global supply chain management market was valued at approximately USD 25.7 billion in 2023 and is projected to reach about USD 78.5 billion by 2033, growing at a compound annual growth rate of 11.8 percent. This growth reflects both opportunity and competitive pressure.
The companies that succeed have learned a fundamental truth. Integration drives performance more than individual optimization ever could.
What is logistics and supply chain management?
Clarity matters here because these terms often get confused in boardroom discussions.
Logistics focuses on execution. Teams manage warehouses, coordinate transportation, and fulfill orders. The work centers on efficiently moving products from point A to point B.
Supply chain management emphasizes strategy. Leaders plan supplier relationships, forecast demand, and design networks that remain resilient under pressure. The focus remains on long-term optimization and risk management.
Both functions matter enormously for organizational success. Yet most companies operate them in isolation, with different reporting structures, separate budgets, and disconnected systems.
This separation creates inefficiencies that appear in quarterly reports. Logistics supply chain management works best as an integrated discipline, not competing departments.
Recent data shows this problem persists. According to A.P. Moller-Maersk, over 76 percent of European shippers experienced supply chain disruption throughout 2024. Nearly a quarter reported more than one significant disruption event.
Consider what happened during early 2020. Store shelves emptied not because transportation failed. Trucks could still move products. The problem was planning. Systems couldn't adapt quickly to sudden demand shifts because logistics and supply chain operated independently.
Key differences between logistics and supply chain management
Understanding these distinctions helps technology leaders allocate resources appropriately.
Logistics teams think operationally. Today's shipments need coordination, warehouse capacity requires management, and customer complaints demand immediate attention. Their metrics focus on cost per shipment, delivery performance, and operational efficiency.
Supply chain teams think strategically. Future demand needs forecasting. Supplier relationships require development. Network resilience demands continuous attention. Their measurements include supplier performance, forecast accuracy, and risk mitigation.
The technology requirements differ significantly between these functions. Logistics needs operational systems. Warehouse management software. Transportation coordination tools. Order processing platforms.
Supply chain management and logistics require planning systems, supplier portals, and analytics capabilities. Most organizations buy these solutions independently and wonder why integration proves difficult.
The organizational design should reflect these different but complementary objectives. Successful companies align both functions under unified leadership with shared performance metrics.
Integrated logistics and SCM: a unified approach
Technology leaders often ask why integration matters more than individual optimization.
The answer lies in system thinking. Optimizing parts independently rarely produces enterprise-wide benefits. Sometimes it creates new problems.
Procurement negotiates favorable supplier terms without considering transportation costs. Demand planning forecasts growth without informing logistics about capacity requirements. Warehouse operations optimize for efficiency without understanding supplier delivery patterns.
These disconnects cost real money. Supply chain logistics management integration eliminates such waste through better coordination and shared information.
The business case for integration includes several compelling elements:
Cost reduction occurs when organizations eliminate redundant processes and optimize entire flows rather than individual components. Companies typically see significant improvements in inventory management, transportation efficiency, and emergency shipment reduction.
Customer experience improves because integrated systems enable accurate delivery commitments and real-time tracking information. Planning and execution alignment means fewer surprises and more reliable service.
Risk mitigation strengthens when both strategic and operational teams access the same information. Supply chain disruptions get identified faster. Response plans execute more effectively.
Integration requires technology platforms supporting strategic planning and operational execution without forcing complete system replacement. This approach respects existing investments while enabling new capabilities.
Innovation in logistics and supply chain
The technology landscape presents both opportunities and challenges for executives.
Vendor marketing often oversells capabilities while underselling implementation complexity. Separating genuinely useful innovation from promotional noise requires careful evaluation.
1. Artificial intelligence
Artificial intelligence delivers value in specific applications. Demand forecasting improves when systems consider weather patterns, economic indicators, and social trends. Route optimization adapts to real-time conditions, including traffic, weather, and driver availability. Predictive maintenance prevents equipment failures rather than simply documenting them.
2. Internet of Things
Internet of Things sensors provide operational intelligence that was impossible previously. Temperature monitoring protects pharmaceutical shipments. Location tracking secures high-value cargo. Equipment sensors enable proactive maintenance scheduling.
3. Automation
Automation handles routine administrative tasks that consume significant time without adding value. Purchase order approvals. Shipment notifications. Vendor communications. Status reporting. These processes benefit from standardization and logistics automation.
4. Cloud-based integration platforms
Cloud-based integration platforms solve connectivity challenges without requiring massive infrastructure investments. Organizations can connect existing systems, automate cross-functional workflows, and provide stakeholder visibility.
Low-code platforms like Kissflow enable business teams to design workflows that match specific operational requirements. Logistics and supply chain management professionals can automate approval processes, coordinate with suppliers, and track performance without extensive IT involvement.
Implementation timelines compress from months to weeks. User adoption improves because teams design their own tools. Total cost of ownership remains reasonable because organizations enhance rather than replace existing systems.
Real-world implementation: McDermott's supply chain transformation
McDermott, a global engineering and construction company operating in over 54 countries, faced a common challenge. Their IT team of six people supported 6,000 business users across Finance, HR, and Supply Chain functions. The workflow backlog kept growing while business users waited months for IT to develop solutions.
Renee Villarreal, Senior Director of IT, implemented Kissflow to enable business teams to build their workflows automation. The platform's intuitive design meant immediate adoption without training campaigns. As one Finance Lead noted: "This is so easy, even my mom could do this. I don't need to call IT to do this. I can do it myself."
The supply chain team quickly automated critical processes, including Marine Operations Approval, Routing Approvals, Invoice Processing, and CAPEX workflows. Within one year, McDermott processed 23,000+ work items through 132 active workflows created entirely by business users.
The transformation eliminated IT bottlenecks while giving supply chain teams direct control over their process improvements. McDermott now aims to standardize all workflows across their global offices using the same approach.
Enterprise challenges requiring attention
Beyond operational efficiency, several strategic issues demand executive focus.
Economic uncertainty adds complexity to these challenges. The World Economic Forum found that 56 percent of leading chief economists expect weaker global economic conditions in 2025, while only 17 percent anticipate improvement. This uncertainty, compounded by geopolitical tensions, increases supply chain risks significantly.
Regulatory compliance
Regulatory compliance varies by geography and industry, and it changes frequently. Organizations should maintain a stricter level of compliance in their operations, even if governments allow for a less-stringent approach. This approach reduces the risk of compliance violations and safeguards supply chains against the enforcement of new regulations.
Sustainability reporting
Sustainability reporting has become a business requirement rather than a nice-to-have initiative. Customers, investors, and regulators expect transparency into environmental impact. This means tracking carbon footprints, supplier compliance, and circular economy initiatives across networks.
Talent management
Talent management represents a significant risk factor. Supply chain expertise often exists in individual knowledge rather than documented processes. When experienced professionals leave, institutional understanding departs with them.
Technology debt
Technology debt accumulates when organizations implement point solutions without considering enterprise architecture. The result includes system sprawl, increased maintenance costs, and reduced organizational agility.
Organizations addressing these challenges effectively treat logistics management and supply chain as integrated business capabilities supported by flexible technology rather than separate functional areas with independent systems.
Future considerations for technology leaders
Several trends will reshape supply chain operations and require technology capabilities.
1. Autonomous decision-making
Autonomous decision-making systems will progress beyond reporting to prescriptive recommendations. These platforms automatically adjust inventory levels, reroute shipments, and negotiate with suppliers based on predefined business rules and learned patterns.
2. Ecosystem orchestration
Ecosystem orchestration will replace traditional linear supply chain models. Instead of managing bilateral relationships, organizations will coordinate networks of partners who share data, risks, and rewards for mutual benefit.
3. Sustainability integration
Sustainability integration will become as important as cost and service performance metrics. Systems must track and optimize for environmental impact alongside traditional key performance indicators.
4. Composable business architecture
Composable business architecture will enable organizations to assemble best-of-breed solutions rather than depend on monolithic platforms. This approach provides flexibility to innovate without legacy system constraints.
Strategic recommendations for implementation
Based on experience across multiple industries, several key considerations emerge for supply chain and logistics management modernization initiatives.
Focus on business outcomes before evaluating technology features.
Define specific capabilities and success metrics before reviewing vendor solutions. Most failed implementations occur because organizations become excited about technology without understanding business requirements.
Design for integration from project initiation.
Avoid optimizing logistics and supply chain functions independently. Maximum return on investment comes from connecting these capabilities and optimizing entire value streams.
Select platforms that support business evolution.
Avoid solutions that constrain organizations within rigid processes. Technology should adapt to changing requirements rather than limiting business flexibility.
Prioritize user adoption alongside system deployment.
Sophisticated technology provides no value if teams don't use it effectively. Change management planning should begin during technology selection, not after implementation.
Organizations that approach supply chain modernization strategically treat it as a business transformation initiative rather than a technology project. They invest in platforms that provide immediate value while building capabilities for future growth.
Platforms like Kissflow enable this approach by providing flexibility to design workflows that match business requirements while integrating with existing technology investments. Results include faster implementation, higher user adoption, and improved business outcomes.
The transformation of supply chain and logistics management will occur regardless of individual organizational preferences. The strategic question involves whether companies will lead this transformation to build competitive advantage or follow industry standards reactively.
Frequently asked questions about logistics and supply chain management
What exactly do logistics and supply chain management involve?
Logistics handles operational execution, including warehouse management, transportation coordination, and order fulfillment. Supply chain management focuses on strategic orchestration, including supplier relationships, demand planning, and network design. Both functions are essential for competitive operations but require different capabilities and performance metrics.
How can businesses improve logistics and supply chain efficiency?
Functional integration results in the highest-impact improvements. Organizations should connect planning and execution systems, align performance metrics across teams, and eliminate manual handoffs between departments. Technology platforms supporting strategic and operational requirements typically deliver better return on investment than point solutions.
What are the main challenges in global logistics and supply chain management?
Strategic challenges include regulatory compliance across multiple jurisdictions, sustainability reporting requirements, talent management and knowledge retention, and technology architecture decisions. These issues require executive attention and long-term planning rather than purely operational solutions.
How does technology improve supply chain and logistics operations?
Technology provides real-time visibility into operations, automates routine processes, and enables proactive decision-making. Value creation comes from improved information quality and faster response capabilities rather than replacing human expertise. Organizations should seek solutions that enhance team capabilities.
How does Kissflow help automate logistics and supply chain processes?
Kissflow provides a low-code platform for designing custom workflows without requiring IT resources. Organizations can automate approval processes, coordinate with suppliers, and eliminate manual handoffs while maintaining flexibility to adapt processes as business requirements change. Implementation typically requires weeks rather than months.
Related Articles
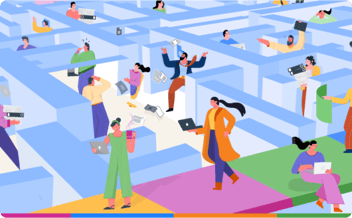
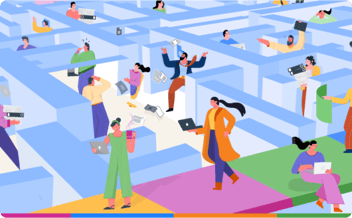