
Your search for
Project Management Procurement HR Finance Procurement
has landed you here. Wondering why?
As a user, you'll experience the full value of Kissflow by implementing it across departments for diverse use cases
rather than just addressing isolated needs like a project management tool for a single team or department.
Kissflow does two things really well
CIO/IT Leaders
If you have a huge backlog of internal applications
and processes to be built
Kissflow is the RIGHT platform
To build custom applications
Automate simple to complex processes
Handle ticketing and support requests
30,000 Hours
Productivity Gained
260%
ROI Achieved
Trusted by
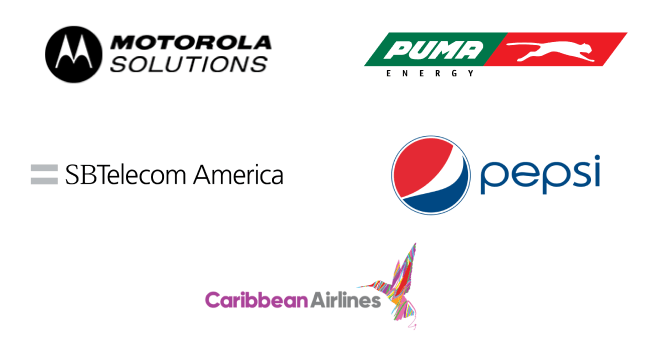
CDO/Transformation Leaders
If you are building a digital-first organization
leveraging citizen development
Kissflow is the ONLY platform that
Users embrace AND IT celebrates
Has the right blend of simplicity and power
Uses Generative AI to reduce the semantic gap
Delivers 10x productivity gains
222,720 Hours
Productivity Gained
$810,000
ROI Achieved
Trusted by
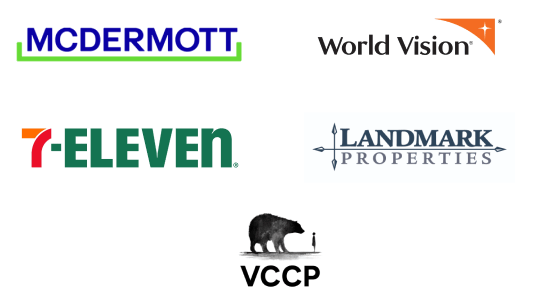
Kissflow does two things really well
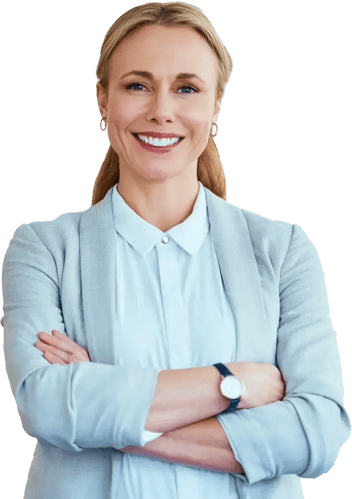
CIO/IT Leaders
If you have a huge backlog of internal applications
and processes to be built
Kissflow is the RIGHT platform
To build custom applications
Automate simple to complex processes
Handle ticketing and support requests
Trusted by

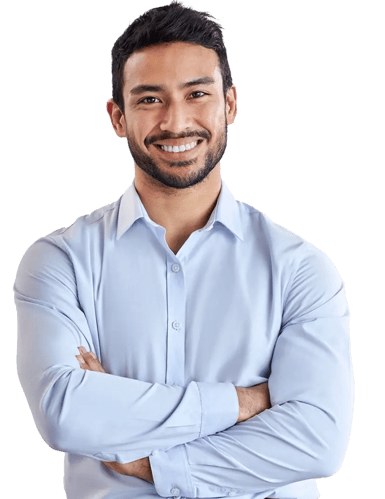
CDO/Transformation Leaders
If you are building a digital-first organization
leveraging citizen development
Kissflow is the ONLY platform that
Users embrace AND IT celebrates
Has the right blend of simplicity and power
Uses Generative AI to reduce the semantic gap
Delivers 10x productivity gains
222,720 Hours
Productivity Gained
$810,000
ROI Achieved
Trusted by

A deep dive into Kissflow's low-code and citizen development features
Low-Code Application Platform (LCAP) |
Citizen Development Platform (CADP) |
---|---|
Primary GoalStreamlining and automating complex business processes, building scalable applications |
Primary GoalEmpowering non-technical users to create simple apps and automate workflows |
Technical Skill RequiredBasic to intermediate coding knowledge |
Technical Skill RequiredNo coding knowledge is required |
Development ApproachIT-led with some business collaboration |
Development ApproachBusiness-led with IT governance and oversight |
Typical ApplicationsEnterprise-grade apps, complex workflows, integrations with existing systems |
Typical ApplicationsDepartmental apps, micro-apps, workflow automation, simple integrations |
Kissflow FeaturesVisual workflow designer, page builder, drag-and-drop interface, pre-built components, API integrations, robust security and governance |
Kissflow FeaturesIntuitive interface, drag-and-drop functionality, pre-built templates, easy collaboration, simplified approval processes |
BenefitsIncreased agility, reduced development time and costs, improved collaboration, enhanced scalability, centralized control |
BenefitsIncreased employee empowerment, faster problem-solving, reduced IT backlog, improved process efficiency, and increased innovation. |
Primary Goal
Streamlining and automating complex business processes, building scalable applications
Technical Skill Required
Basic to intermediate coding knowledge
Development Approach
IT-led with some business collaboration
Typical Applications
Enterprise-grade apps, complex workflows, integrations with existing systems
Kissflow Features
Visual workflow designer, page builder, drag-and-drop interface, pre-built components, API integrations, robust security and governance
Benefits
Increased agility, reduced development time and costs, improved collaboration, enhanced scalability, centralized control
Primary Goal
Empowering non-technical users to create simple apps and automate workflows
Technical Skill Required
No coding knowledge is required
Development Approach
Business-led with IT governance and oversight
Typical Applications
Departmental apps, micro-apps, workflow automation, simple integrations
Kissflow Features
Intuitive interface, drag-and-drop functionality, pre-built templates, easy collaboration, simplified approval processes
Benefits
Increased employee empowerment, faster problem-solving, reduced IT backlog, improved process efficiency, and increased innovation.
Don’t take our word for it
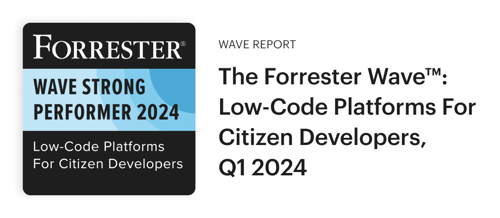
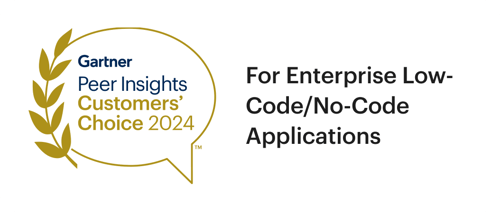
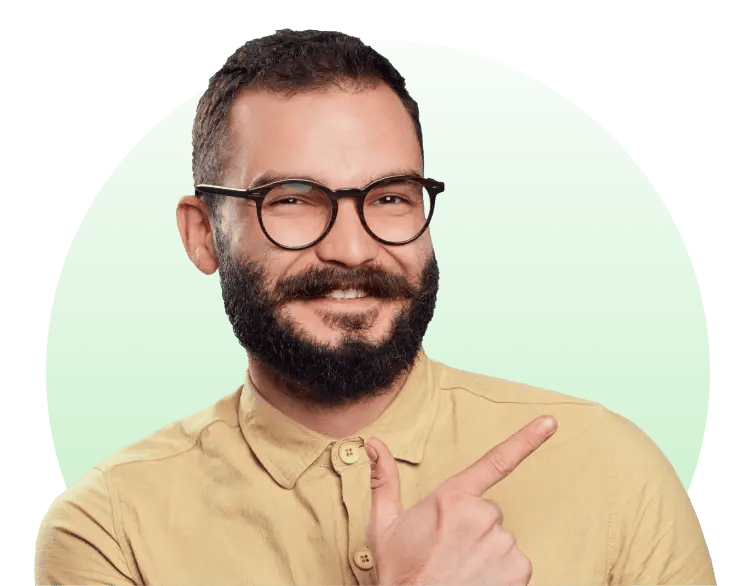
Market Leaders in the G2 Grid for 2024
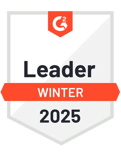
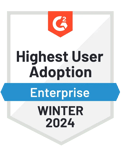
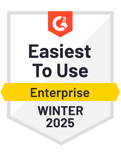
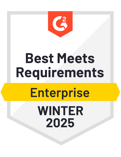
Pricing starts at
$1,500 /month
Talk to our Solution Architect to see if Kissflow is the right platform for you
By signing up, I accept the Kissflow Terms of Service and Privacy Policy
Thank you for your interest in exploring Kissflow. Our solution experts will get in touch with you within one business day.